In precision-driven environments like laboratories and healthcare settings, the right robotic wheels determine the mobile robot’s speed, maneuverability, and stability. These characteristics directly impact operational efficiency – whether it’s reliable transport of sensitive specimens or ensuring hygienic floor cleaning without disrupting vital workflows.
AMR robots introduce the potential to streamline tasks, reduce human error, and enhance safety in these demanding sectors – and it all starts with their types of wheels
Table of Contents
1.
Key Considerations for AMR Robotic Wheels
Selecting the right wheels for your autonomous robot requires a careful analysis of the tasks it will perform, the environment it must navigate, and the level of maneuverability required. Mismatched wheels can lead to inefficient operation, potential floor damage, and even safety concerns. Let’s delve into the three most critical aspects to evaluate:
Intended Function
First, define the autonomous robot’s primary purpose—this will heavily influence wheel choice. Consider:
- Material Transport: Will the robot move delicate medical samples, heavy boxes, or large, bulky items?
- Delivery: Where does it need to go? Labs might require tight navigation around equipment, while a hospital may have long hallways to cover.
- Cleaning: What type of cleaning? Will the robot sweep, scrub floors, or apply disinfectant?
Environment
The AMR robot’s work environment plays a huge role in wheel selection. Ask yourself:
- Floor Surfaces: Are they smooth concrete, industrial carpet, slippery tile, a mix of these, or primarily outdoors?
- Obstacles: Does the robot need to maneuver around furniture, tight corners, or thresholds between rooms?
- Inclines: Are there ramps or sloped floors it must navigate?
Movement Capabilities
Finally, consider the specific movements essential for the AMR to succeed. Think about:
- Omnidirectional Motion: Does it need to move sideways or rotate on the spot for maximum agility in tight spaces?
- Precise Turning: Is pinpoint accuracy needed (like aligning with lab equipment)?
- Outdoor Capability: Will the robot ever go outside where it faces uneven terrain or weather?
2.
Common Robot Wheel Types
Choosing the right robot wheels means finding a balance of maneuverability, stability, cost, and power efficiency. Each wheel type comes with specialized advantages and trade-offs, so let’s analyze the most popular choices for autonomous robots.
Differential Drive (Standard Wheels)
These are your most basic wheels, with two main wheels fixed to an axle. Similar to a car’s front wheels – an axle steers and provides motion, but primarily moves the robot forward or backward.
![[B] AMR Wheels - Differential Wheels Diagram of differential wheels for an autonomous mobile robot AMR](https://www.quasi.ai/wp-content/uploads/2024/04/B-AMR-Wheels-Differential-Wheels-750x564.jpg)
Pros:
Performs very well on tasks requiring movement in primarily straight lines.
- Cost-effective: Their simple design makes them affordable to manufacture and maintain.
- Energy-efficient: Great for long, linear movements with minimal directional changes.
- Mechanically simple: Easy to repair and troubleshoot, reducing downtime.
- High speed potential: Covers long spans of distance quickly in the right environment.
Cons:
Struggles in tight spaces or where precision is crucial.
- Poor on uneven surfaces: Unable to make precise turns or navigate tight spaces.
- Limited maneuverability: Can get stuck on obstacles or uneven flooring.
- No omnidirectional ability: No way to move sideways or rotate on the spot.
- Prone to slippage: Can lose traction on slick surfaces, impacting accuracy.
Robots That Benefit Most from Differential Drive
- Warehouse transport robots: Long aisles, predictable routes, and a focus on carrying loads efficiently create an idea environment for AMRs with standard wheels and robust weight-capacity to excel .
- Basic delivery robots in simple environments: This includes environments with uncomplicated floorplans with primarily straight-line tasks.
- Support tasks in non-critical areas: Moving non-sensitive items where precision isn’t crucial.
Robots That Benefit Least from Differential Drive
- AMRs in labs or hospitals: Require tight turns, precise movements, and the ability to navigate around equipment and people.
- Robots needing omnidirectional movement: Tasks like aligning with machinery or moving sideways in tight spaces are impossible with standard wheels.
- Outdoor robots: Uneven terrain and obstacles make standard wheels a poor choice.
Caster Robotic Wheels
These are the familiar swiveling wheels you find on shopping carts or office chairs. Picture small wheels attached to a vertical mount that allows them to rotate freely in any direction. They’re frequently They’re, and are simple and cost-effective. But, they don’t turn well in tight spaces.
![[B] AMR Wheels - Caster Wheel Caster wheel that may be found on an autonomous mobile robot AMR to allow for](https://www.quasi.ai/wp-content/uploads/2024/04/B-AMR-Wheels-Caster-Wheel.jpeg)
Pros:
Easy, frictionless movement on clear, long, straight distances.
- Smooth on flat surfaces: Glides effortlessly on smooth, even floors.
- Cost-effective: A simple, readily available, and budget-friendly solution.
- Omnidirectional potential: While not on their own, caster can combine with other wheel types to allow sideways motion.
- Good for pre-set paths: If the route is simple enough, casters can be reliable.
Cons:
Less stable and reliable and cannot handle bumps, obstacles, or tight turns.
- Prone to getting stuck: Issues with small obstacles and chanding surfaces/floor type.
- Unstable at higher speeds: Produces wobbling with heavier loads.
- Limited maneuverability: Cannot provide precise turning in any configuration.
- Requires smooth, clean floors: Any debris or imperfection make caster wheels unpredictable.
Robots That Benefit Most from Caster Wheels
- Lightweight Cleaning Robots: Only on smooth surfaces and with basic movements – so as basic sweeping robots, but not as more complex disinfection robots
- Wheeled Carts & Equipment: Benefit from the casters’ smoother ride to ensure undamaged delivery.
Robots That Benefit Least from Caster Wheels
- AMRs in Labs and Healthcare environments: Facilities with uneven surfaces and dynamic are a poor fit for caster-only robots.
- Robots needing precise control: Casters lack the precision for close alignment or tight navigation.
- Outdoor and Heavy-Duty AMRs: Heavier loads and terrain variations need much more stability than caster wheels provide.
Mecanum Robotic Wheels
These unique wheels feature a set of rollers, set at 45-degree angles along the circumference. This angled design allows for omnidirectional movement with precise control, including sideways and diagonal motion.
In use-cases such as the Quasi Model R2 AMR Manipulator Robot, mecanum wheels combine with high-torque motors to enable all-direction movement that allows intricate maneuvering in tight spaces and dynamic environments.
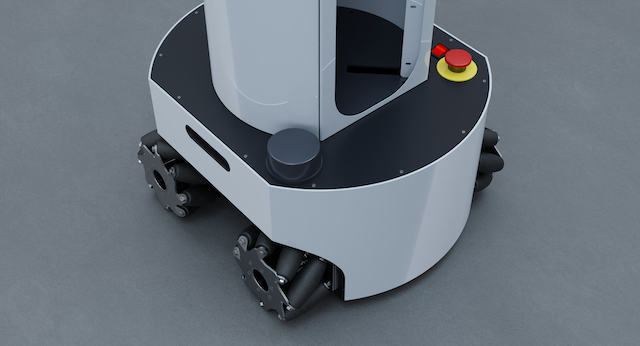
Pros:
Agility in confined spaces and on-the-spot turning for perfect alignment.
- High maneuverability: Lets robots move in any direction without turning – ideal for tight spaces.
- Precise control: Allow robots toexecute intricate maneuvers, including tight turns and alignment with equipment.
- Significant efficiency: The ability to move without constant reorientation can reduce task completion times.
- Well-suited for constrained environments: Mecanum wheels excel in areas where traditional wheels lack the necessary agility.
Cons:
More complex with high expense and energy consumption.
- Mechanical complexity: Design is more complex, with higher cost and maintenance.
- Energy consumption: Rollers’ constant directional changes uses more power than simpler wheels.
- Less optimal for long, straight distances: Capable of linear motion, but mecanum wheels’ strength lies in maneuverability, not pure speed.
- Configuration required: Fully utilizing mecanum wheels often requires advanced programming.
Robots That Benefit Most from Mecanum Wheels
- Lab & hospital AMRs: Provide the highest level of control for safe navigation throughout sensitive environments.
- Robots for precise positioning: Ideal in tasks involving alignment with machinery or charging stations.
- AMRs in tight workspaces: Warehouses with narrow aisles, complex factory floors, crowded doctors’ offices, or busy biobanks.
- Robots that need flexible movement: If tasks require movements and turns difficult for standard wheels, mecanum wheels hold significant advantage.
Robots That Benefit Least from Mecanum Wheels
- Outdoor robots: Mecanum wheels aren’t well-suited for uneven terrain or exposure to the elements.
- Robots that execute simple tasks in open spaces: The added cost and complexity may not be justified if extreme maneuverability is unnecessary.
- Robots that need speed or energy efficiency: Mecanum wheels aren’t best for long distance or economic performance
Omni Robotic Wheels
Omni-wheels consist of small rollers mounted perpendicular to a larger wheel’s circumference. This enables lateral (sideways) motion in addition to the usual forward and backwards, making these wheels useful for precise movements in tight spaces.
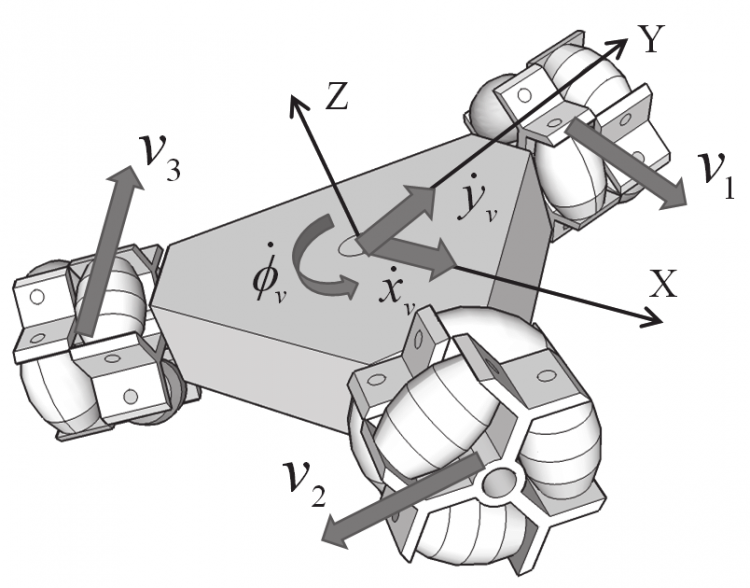
Pros:
Good for sideways movement (like on a conveyor belt) in tight spaces and has the possibility of omnidirectional movement.
- Lateral movement: Able to move sideways, for maneuverability in tight spaces.
- Potential for omnidirectional capability: When combined with the right configuration (3+ wheels), true omnidirectional movement like with mecanum wheels is possible.
- Useful in specific applications: Niche uses find their particular movement ideal for agriculture and lawnmower robots.
Cons:
Stability is reduced for straight travel and overall efficiency depends on floor type.
- Reduced stability with heavy loads: Design is more complex, with higher cost and maintenance.
- Not ideal for long-distance or high-speed travel: Best suited for short movements where precision is prioritized.
- Less efficient on smooth surfaces: Rollers create friction and resistance when moving in a straight line.
- Surface/floor sensitivity: Performance is affected by floor type – too smooth leads to slippage, too rough creates jerking.
Robots That Benefit Most from Omni Wheels
These include AMRs with alignment needs in tight spaces next to equipments and machinery; Service robots assisting with intricate tasks; Hobbyist or competition robots.
- Small package sorting robots in warehouses : Omni wheels allow precise lateral adjustments for aligning packages on conveyor belts or diverting them to the correct output line.
- Assistive robots in healthcare: A robot arm on an omni-wheel base can reposition itself for better access and tool manipulation in tight spaces.
- AMRs operating indoors in tight spaces: Examples include warehouses with narrow aisles, complex factory floors, doctors’ offices, and busy biobanks.
- Small-scale robots with extreme maneuverability needs: Often seen in hobby robotics or competitions where navigating mazes is a factor.
Robots That Benefit Least from Omni Wheels
- AMRs needing to carry heavy payloads : lack of stability is a significant drawback for heavy transport.
- AMRs focused on long-distance travel or speed: The added cost and complexity may not be justified if extreme maneuverability is unnecessary.
- Outdoor robots: Uneven terrain and unpredictable surfaces make omni wheels unreliable.
- AMRs where omnidirectional movement isn’t crucial: If the primarily tasks are basic, the cost and limitations of omni wheels may not be justified.
3.
Case Study: Mecanum Robotic Wheels in the Lab
Featuring the Quasi Model R2 Robot
Laboratory, research, and healthcare spaces pose unique challenges for deployment of an autonomous mobile robot (AMRs) fleet:
- Limited Maneuvering Space: Tight corridors and expensive equipment demand precise movement with a quick obstruction response time.
- Contamination Control: Sterility requirements of critical samples and materials demand smooth, controlled movements.
- Workflow Adaptability: To provide long-term ROI, mobile robots must readily adapt to changing lab layouts, equipment configurations, and research protocols to provide long-term value.
The design of the Quasi Robotics’ Model R2 AMR Manipulator was focused directly on addressing these challenges. The incorporation of mecanum wheels was optimal for superior maneuverability in compact and demanding environments.
At Quasi, mechanum wheels pave the way for more flexible lab automation – AMRs with agile, on-the-spot navigation could enable smaller, reconfigurable workspaces. By optimizing space utilization and freeing up skilled labor, such mobile robots would enable labs to maximize the value of both their equipment and research personnel.
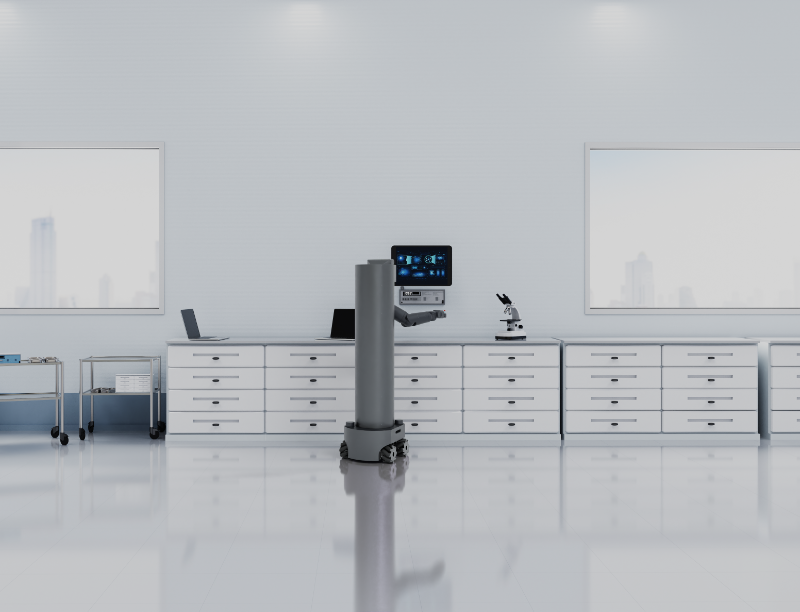
Key Advantages of Mecanum Robotic Wheels
- Omnidirectional Movement: Enables movement and on-the-spot rotation in any direction without the need for reorientation.
- Precision Navigation: Ideal for tight spaces and accurate positioning near lab equipment.
- Controlled Motion: Minimizes vibration and abrupt movements, reducing the risk of sample disruptions or collisions.
- Workflow Flexibility: Omnidirectional capability allows the R2 to easily adapt to changing workflow layouts, saving time and minimizing reprogramming needs.
Real-World Application: Blood Sample Transport with Model R2 AMR
The mecanum wheel design of the Quasi Model R2 supports fast, reliable transport of blood samples to labs for timely analysis.
Safety & Compliance:
- The precision enabled by mecanum robotic wheels reduces collision risks, protecting staff and patients, while also safeguarding valuable equipment and samples.
- Mecanum wheels enable integration with various safety sensors which allow the robot to autonomously stop if it encounters an unexpected person or object in its path. This added layer of safety helps the R2 operate smoothly alongside human staff while enhancing compliance with laboratory safety protocols.
Adaptability:
- With omnidirectional capabilities, the R2 can be re-tasked with new routes on the fly, responding rapidly to urgent blood sample transport needs throughout the facility.
- Mecanum wheels eliminate the need for complex turning maneuvers in the software, streamlining route changes and minimizing the time it takes the R2 to adapt to dynamic hospital environments.
Timeliness & Reliability:
- The R2’s ability to navigate efficiently through crowded spaces is supported by its automatic wheels, reducing transport time, ensuring samples reach the lab quickly for accurate and timely analysis.
- Each mecanum robot wheel contributes to overall reliability, reducing the risk of downtime due to collisions or navigation issues, making the R2 a crucial link in the patient care chain.
4.
Conclusion
Choosing the right robot wheels for your AMR is not a one-size-fits-all solution. The most effective approach is to carefully align your wheel selection with the robot’s specific tasks, the environment it navigates, and your desired efficiency goals. If you seek expert guidance in optimizing your robotics investment, Quasi Robotics specializes in finding the ideal robotic solutions that match your operational needs, including helping you choose the perfect robot wheels.
Discover how Quasi Robotics and its intelligent autonomous robots can transform your facility – visit our website to learn more.