Addressing Laboratory Challenges
with Autonomous Mobile Robots (AMRs)
Robotic Process Automation (RPA) in life sciences marks a significant evolution in laboratory and research methodologies, addressing critical challenges that have long impeded progress in these fields. Prolonged sample processing, staffing shortages, and integration difficulties have notably escalated since the COVID-19 pandemic. The result has been delays in whole-lab procedures, impacting research timelines and raising concerns over the precision and reproducibility of scientific results.
The recent introduction of mobile collaborative robots, including new entrants like Quasi Robots, represents a significant advancement in lab automation. These robots offer novel solutions to the aforementioned challenges, bringing enhanced efficiency, precision, and adaptability to laboratory operations.
Challenge 1: Prolonged Sample Processing Time
Laboratories, especially those in the fields of biomedical research and diagnostics, operate within a stressful paradox; they’re faced with an ever-growing demand for rapid results, simultaneously coupled with the absolute necessity of maintaining accuracy.
This incongruence became especially apparent and continues to track particularly since the COVID-19 pandemic, with many labs experiencing:
Increased Demand for Testing:
- An unprecedented surge in viral detection became critical – for individual patients and for broader epidemiological insights and public health interventions alike.
- Existing sample processing workflows just couldn’t keep up, resulting in processing bottlenecks, testing delays, and even compromised decision-making.
Impacted Research Timelines:
- Testing and sample processing delays are often followed with resulting delays in time-sensitive research and clinical trials.
- The result is postponement of publications containing crucial findings and ultimately hindrance to the development of novel medicines and processes.
Scrutiny Over Precision and Reproducibility:
- Manual processing techniques are prone to variability, impacting the precision and reproducibility of experiments and raising concern about research validity.
Challenge 2: Staff Shortages and High Turnover
While staff shortages and high turnover may not be new to the laboratory setting, the global pandemic has amplified these challenges to the point of urgency. The need for skilled laboratory personnel has widened the gap between demand and availability, creating a critical bottleneck that threatens efficiency and accuracy in crucial clinical and research work.
Workforce Fatigue and Burn-Out:
- Understaffed laboratories inevitably place heavier workloads on remaining employees.
- This increased pressure can lead to a cycle of exhaustion, decreased morale, and ultimately, higher turnover rates.
Widening Skill Gap:
- Understaffed laboratories inevitably place heavier workloads on remaining employees.
- This increased pressure can lead to a cycle of exhaustion, decreased morale, and ultimately, higher turnover rates.
Training Burden:
- The constant cycle of new hires resulting from high turnover consumes both time and resources dedicated to training and onboarding.
- This investment detracts from core laboratory functions and slows down overall productivity.
Challenge 3: Interoperation of Robotic Automation and Existing Systems
Though robotic applications may hold immense promise for future lab operations, seamlessly integrating multiple automated systems into varying laboratory environments presents its own set of challenges. Full integration of lab process participants avoids disruptions, optimizes workflows, and unlocks the full potential of automation within the laboratory.
Compatibility with Existing Systems:
- Understaffed laboratories inevitably place heavier workloads on remaining employees.
- This increased pressure can lead to a cycle of exhaustion, decreased morale, and ultimately, higher turnover rates.
Managing Diverse Sample Types:
- Laboratories handle a diverse array of sample types, each with unique handling requirements.
- Designing automation solutions that effectively accommodate this variety, without compromising sample integrity or compromising analytical accuracy, is crucial.
Standardizing Data Flow:
- Collaborative and organized data management across all research workflows and testing trials is critical to lab operations success.
- Automation systems should seamlessly integrate with existing data management software, enabling real-time tracking, analysis, and interpretation of experimental results.
Early Beginnings
(1950s-1980s):
Laboratory workflows underwent a fundamental transformation as manual, repetitive tasks were gradually delegated to basic mechanized systems. The first instances of automation in labs possessed limited capabilities and relied on simple mechanical principles – often resembling the assembly line factory robots they had been based on.
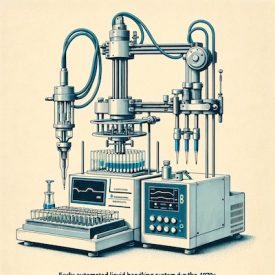
These early pioneers, primarily focused on liquid handling. And despite their rudimentary nature, they marked a significant departure from traditional methodologies, laying the groundwork for future efficiency and standardization. Their development, however, faced considerable challenges due to the nascent state of robotics and computing technology.
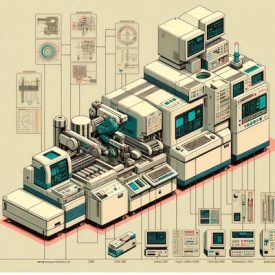
The Rise of Microprocessors and Computers
(1980s-2000s):
In the 1980s, integration of microprocessors and early computer systems allowed for more precise control over lab equipment and expanded their task ability range.
This period saw the development of automated analyzers, robotizing various analytical techniques like spectrophotometry and chromatography.
Programming and control software became integral, allowing researchers to manage more of their workflows and processes, various tasks with greater precision and throughput. Early robotic arms also made their debut, offering increased flexibility and automation potential compared to the previous generation of fixed-function instruments.
Integration of Robotics and Advanced Computing
(2000s-Present):
Modern lab automation includes a combination of advanced robotics and high-performance computing platforms, creating more interconnected, efficient lab environments.
Research facilities now house advanced robotic arms with enhanced precision. Advanced algorithms can analyze huge datasets, extract patterns, and highlight valuable insights. Machine learning allows robots to employ real-time decision-making and even autonomous research endeavors.
All of these advancements have led to a higher throughput of screening and collection than ever before – with robots enabling enormous amounts of samples to be tested in incredibly short periods. The impact of this lab automation extends beyond efficiency – it enables groundbreaking discoveries and advancements around the world.
New Focus of Lab Automation: Mobility
Historically, laboratory automation has focused on larger, stationary, single-purpose robots for automating specific tasks in the research workflow. Manual intervention and machine tending was often required for tasks involving material transport and relocation, increasing labor costs and introducing potential for human error.
A new area for innovation has now emerged – primarily as a response to new environmental and industry atmospheres:
- Increased Demand for Efficiency: Growing complexity of scientific research and pressures for faster results required laboratories to find more efficient ways to handle repetitive tasks.
- Labor Shortages and Ergonomic Concerns: Shortages in skilled labor and concerns over worker safety need for automated solutions that can handle mundane, physically demanding tasks.
- COVID-19 Pandemic Response: Adequate sample management helps in adhering to regulatory standards and protocols, which is essential in clinical and research settings.
- Supports Data Analysis: Social distancing requirements created a need for remote and automated operations in labs to reduce human contact.
To address these ongoing shifts, facilities are now turning to flexible mobile automation to fill the gaps of rigidity and bottlenecking in sample and material movement. Particularly, they look toward mobile pick and place robots and transport carts, like the Model R2 and Model C2, offered by Quasi Robotics.
Two Types of Robotics for Research Laboratory Automation
Autonomous Mobile Transport Carts: These machines are designed for material, sample, and equipment movement. They rely on tech including sensors, cameras, and navigation systems to transport and deliver items autonomously within a lab environment.
- Their adoption has been driven by the need to increase efficiency and reduce manual workload in transporting samples, reagents, and other materials. In life science labs, where the movement of sensitive materials is frequent, these carts enhance workflow efficiency and reduce the risk of human error.
- Robotic carts are becoming more popular as labs move towards fully automated systems, where human intervention is minimized.
Mobile Pick and Place Robots: These machines combine the capabilities of traditional, stationary robotic arms with the self-navigation of an AMR. This allows them to perform tasks at multiple locations within a lab.
- This capacity for movement elevates a standard pick and place robot to operate beyond the limitations of arm and gripper reach.
- As a response to the growing complexity of laboratory workflows, mobile pick and place bots aren’t confined to a single workstation. Instead, they allow more flexible and dynamic lab setups, where the robot can transition between tasks and stations as needed.
Both robotic delivery carts and mobile manipulator robots are becoming more popular in lab and research settings. They offer increased flexibility, efficiency, and can be more easily integrated into existing lab environments to accomplish more variety of tasks than their stagnant predecessors.
Quasi Autonomous Robots: Designed for Research Workflows
The landscape of laboratory automation is steadily evolving, seeking improved efficiency and adaptability to address contemporary challenges. Among emerging players, Quasi Robotics stands out with its innovative custom robots, Model C2 and Model R2, designed to specifically tackle key pain points in laboratory workflows.
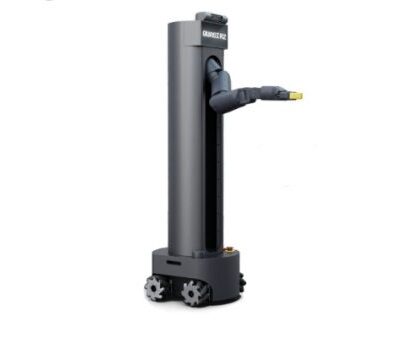
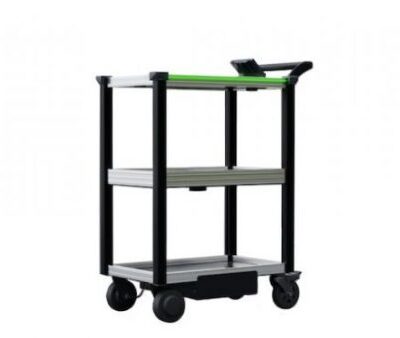
Model R2
Autonomous Mobile Manipulation
The Model R2 handles precision pick and place tasks with autonomous mobility built in, offering dexterity in manipulation without reach limitation. With customizable tools and functions, the R2 is particularly beneficial in handling delicate or hazardous materials, reducing risk to personnel and ensuring accuracy of these tasks.
Model C2
Autonomous Mobile Item Transport
The Model C2 is an autonomous mobile robot specializing in the reliable robotic delivery of samples, vials, material and lab equipment. Designed with laboratory workflows in mind, C2 specifically addresses time-wasting tasks related to repetitive movement, logistical inefficiencies, and traceability inadequacies of the research process pipeline:
Challenge 1:
Accelerating Sample Processing Time
With AMR automation, processing time is decreased, testing demands are better met, research timelines are maintained and reliability in the facility’s research outcomes is bolstered:
Autonomous Mobile Transport Cart:
- Reduces the need for manual transport of samples and materials, allowing existing staff to focus on more complex tasks.
- Provides a consistent level of performance, mitigating the impact of staff turnover on lab operations.
Mobile Pick and Place Robot:
- Automates repetitive tasks such as sample sorting and preparation, reducing the demand for specialized manual skills.
- Helps maintain operational continuity in the face of staff shortages by performing tasks that would otherwise require human intervention.
Challenge 2:
Empowering Staff During Labor Shortages
By incorporating AMR robotics, employees are empowered to focus on advancing their skills, directing their energy and focus toward research opportunities, and utilizing their energy towards analytical tasks that improve experiment results.
Autonomous Mobile Transport Cart:
- Reduces the need for manual transport of samples and materials, allowing existing staff to focus on more complex tasks.
- Provides a consistent level of performance, mitigating the impact of staff turnover on lab operations.
Mobile Pick and Place Robot:
- Automates repetitive tasks such as sample sorting and preparation, reducing the demand for specialized manual skills.
- Helps maintain operational continuity in the face of staff shortages by performing tasks that would otherwise require human intervention.
Challenge 3:
Integrating Automation Robots w Existing Systems
Autonomous Mobile Robots are increasingly being designed to offer simple integration via mobile robot platforms and cloud robotics. This allows them to sync seamlessly with a variety of existing lab equipment and software platforms.
Autonomous Mobile Transport Cart:
- Can be integrated with laboratory information management systems (LIMS) for seamless tracking and management of samples.
- Often designed to be compatible with a variety of laboratory layouts and equipment, ensuring smooth integration into existing workflows.
Mobile Pick and Place Robot:
- Equipped with advanced sensors and control systems, can be programmed to work alongside existing laboratory equipment.
- Can be customized or configured to handle different types of samples and containers, aligning with the specific needs of various lab processes.
The combination of an autonomous mobile transport cart and a mobile manipulation pick and place robot offers a comprehensive solution to address prolonged sample processing times, staff shortages, and the need for integration with existing systems. These technologies enhance efficiency, reduce manual labor, and support a more streamlined, productive, and resilient laboratory environment.